Manufacturing Process
Standard Steel Ball Production

Call us today at 860-210-0808 to learn more about Global Precision’s industries served and the various market applications for our high-quality steel, ceramic, and glass balls and rollers!
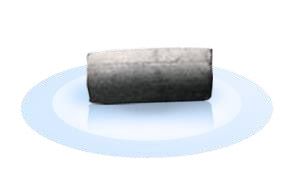
1. Heading
Ball blanks are cold or hot headed from rolls of wire or bar stock depending on their size and the material. The heading machine cuts off a short cylinder of the material and a moving die with a concave spherical cup drives the cylinder into a matching cup in a fixed die. The result is a spherical shape which is the ball blank.
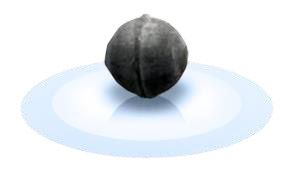
2. Flashing
The flashing operation removes the slight belt and small protrusions left on the surface faces by rolling them between the two hard alloy plates under high pressure.
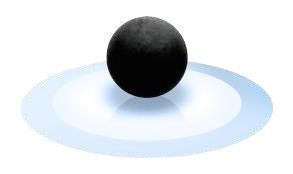
3. Heat Treat
The balls are hardened, if required, by heating them to a high temperature (over 1500 degrees Fahrenheit) in an atmospherically controlled furnace and then quenching them into a liquid bath. They are then tempered to reduce their brittleness by heating them to a low temperature (around 325 Fahrenheit). Samples are checked for hardness. The grain size and metallurgical structure are inspected under a high power microscope.
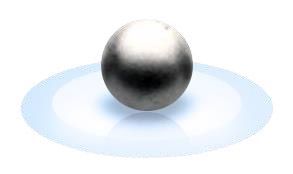
4. Grinding
The hardened balls are precision ground by rolling them between the faces of a fixed iron plate and a very hard fine-grit grinding wheel.
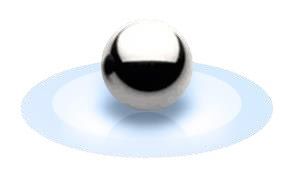
5. Lapping/Polishing
The next step is the lapping operation. The hardened ground balls are rolled between two cast iron plates. One plate is fixed while the other is rotated at a very low speed. The real secret of the extreme quality of precision balls happens here. At this stage the sphericity and size have been established and are carefully inspected by ABMA customer requirements. The final production operation is polishing which adds the shiny luster to the finished ball. The balls are then inspected visually and / or mechanically inspected.